Separation of hydrocarbon liquids and gasses from water and sediments is a challenging operation. Optimal oil and gas separator performance can only be attained through highly reliable and accurate monitoring of multiple parameters, including temperature, pressure, level, flow, and interface. When distinct interfaces give way to continuous graduation, measurement can become highly complex, reliant upon expert know-how and applied technologies. We combine both for optimal separation performance.
Dữ kiện chính
2,200
USD/ day
is the number of dollars spent in a day for demulsifiers
Learn how you can increase separation process efficiency

Heavy and extra-heavy crude oil separation*
Traditional measurement technologies present limitations in the separation of heavy and extra heavy crude oil, not only due to their inability to provide complete process data. The need to install these technologies within the separator renders them vulnerable to contamination.
*Heavy: > API 10 - 22,3 (> 920 kg/m³) Extra heavy: < API 10 (> 1000 kg/m³)
Our expertise in the field
Installed outside the separation vessel, the Endress+Hauser Gamma Density Profiling System is a preferred solution for heavy and extra-heavy crude oil separation process monitoring.
- Avoid measurement inaccuracies caused by contamination and build-up
- Ensure separation process continuity
- Reduce operating costs

Medium crude oil separation*
The medium crude oil separation process is rendered complex by the necessity to accurately measure both the overall level as well as the interface, impossible with a single device. Moreover, an emulsion layer is often present, and if it exceeds 5cm (2 inches) in depth, a standard guided-wave radar device will be unable to measure the interface.
*Medium: API 31.1 - 22.3 (870 - 920 kg/m³)
Our expertise in the field
Endress+Hauser has developed technologies specifically designed to overcome the unique challenges of the medium crude oil separation process.
- Simplify medium crude oil separation with a single device
- Monitor the interface through any emulsion layer with our multi-parameter guided wave radar technology
- Minimize process downtime and reduce operating costs
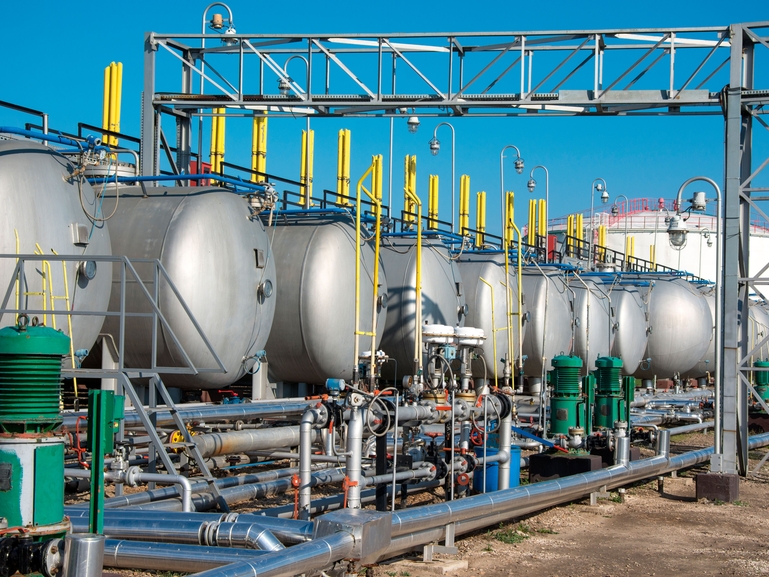
Light crude separation*
Most of today’s horizontal light oil separators are equipped with mechanical level and/or density control devices. Mechanical devices present limitations, necessitating both specific adaptations depending on the API of the oil that needs to be measured, and regular ongoing maintenance.
*Light: API 45 - 31.1 (< 870 kg/m³)
Our expertise in the field
Leveraging guided radar level measurement, Endress+Hauser instrumentation overcomes the limitations of mechanical devices to optimize the separation process for light crude oil.
- Deploy Levelflex FMP55, the new standard in interface measurement
- Avoid downtime for instrumentation adaptations when switching output
- Reduce ongoing operating and maintenance costs
Benefits
Extracting maximum resources is your primary concern - supporting you in that process is ours. Our process automation solutions help you maintain safe, efficient and clean operation. As well, when a valuable member of your team retires, the knowledge acquired is not always easy to replace. This is why our service organization can assist you in filling personnel gaps with inspection, commissioning, engineering, and calibration services, as well as with training programs for future employees.
Dữ kiện chính
300+
radiometric interface measurement and Density Profiling systems installed worldwide
Dữ kiện chính
8,500l
of demulsifiers saved in a year, which corresponds to 10%
Dữ kiện chính
5%
reduced risk of foaming inside a separator
How we can help
Providing a wide portfolio of highly dependable, class-leading measurement technologies covering process variables at every stage, Endress+Hauser enables effective control of oil, water, gas and sand separation.
- Identify liquid and sediment layer locations and thicknesses, optimize demulsifier and anti-foam agent injection
- Open standards for ease of integration and control flexibility
- Easy retrofit for profiler solution
- Ensure compliance with environmental standards